
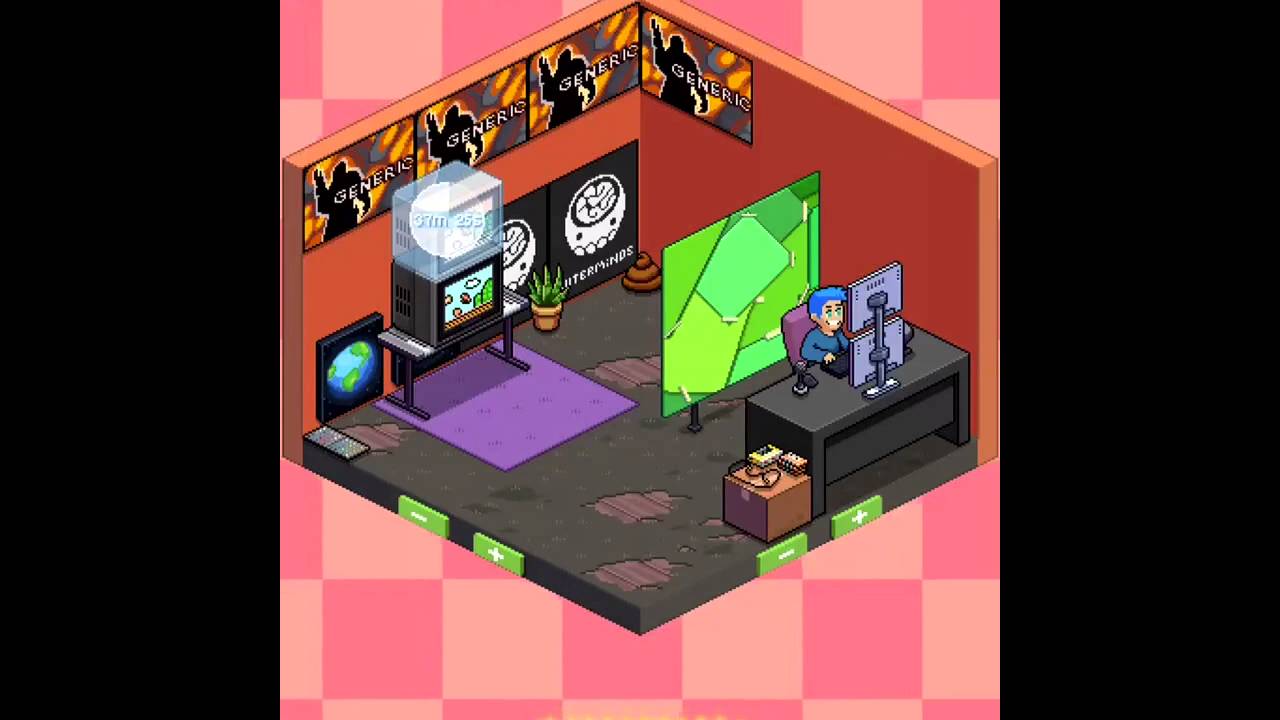
Around 100 m² vacuum-pipe-collectors (55.8 m²ap), which were installed on the south facade (as the picture shows), provide the heat. Now at sunny summer days the solar system reduces the gas demand for the cleaning process by approx. The heat demand for this cleaning process is around 200 MWh/a.īefore the solar process heat plant was taken into operation in April 2014, the heating of the required fresh water was done by heat recovery and a gas boiler. For that final cleaning, the complete production equipment has to be lathered with a cleaning solution and thoroughly rinsed with more than 10 m³ of hot water, to remove fats, sugar and further contaminants. Due to the products, predominantly cream and sugar residues remain on the production line and the tools those residues have to be completely removed after each production day due to reasons of hygiene. Currently 100 employees work at the Hack Gastro-Service oHG, 75 of which work directly in the production.ĭue to the products, predominantly cream and sugar residues remain on the production line and the tools those residues have to be completely removed after each production day due to reasons of hygiene. Currently 100 employees work at the Hack Gastro-Service oHG, 75 of which work directly in the production.

A very important product group are cream-cakes for which more than 4 tons of cream is processed daily. The subsidiary of the Hack AG from Kurscheid produces frozen and fresh baked goods.

Thanks to the installation of vacuum-tube-collectors at their facade, the Hack Gastro-Service oHG saves a lot of energy in the cleaning process.
